Mill Creek Provides IO for Munroe-Meyer Institute in Omaha
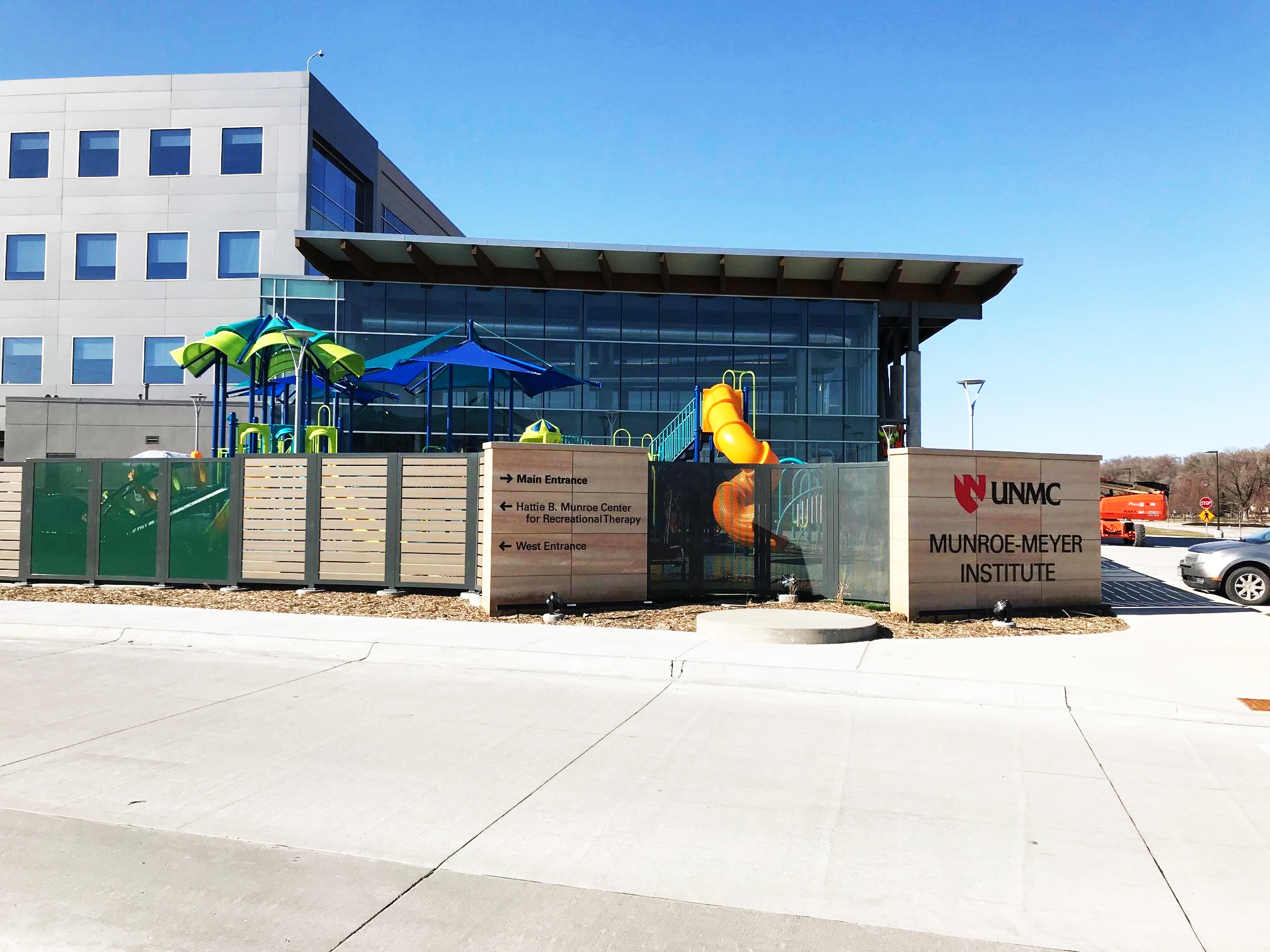
The Munroe-Meyer Institute’s new replacement facility in Omaha opened in June this year, with more than double the size of MMI’s former home, providing essential space for department growth.
The new facility includes:
- Dental, optical and healthy nutrition and wellness clinics, including an optical shop, a panoramic X-ray machine and three negative-pressure dental rooms
- Integrated Center for Autism Spectrum Disorders (iCASD) with six early intervention classrooms
- Accessible play spaces inside and out and an indoor splash pad
- Dedicated maker space that includes a 3D printer, precision cutting and drilling devices, soldering equipment and other tools
- Family resource area
- A kiln for recreational therapy art programs
- Soundproof audiology booth
- Two pools with a water slide and water volleyball net
- Gym and exercise areas
- Outdoor vegetable garden for classes or relaxation and skill development.
- Clinic areas, including the iCASD, which provide families with carefully considered, sensory-friendly environments and spaces
- Clinical rooms with adjustable colored lighting
- Observation areas
- A larger sensory-motor laboratory
- Virtual reality lab that will include an omnidirectional treadmill, which lets a person move in any direction
- Outdoor plaza with sculptures, benches, and picnic tables
- Meditation room
- Sheltered “escape coves”
- Simulated apartment space with a kitchen area, living space, bedroom and accessible bathroom, which allows people to work on independent living skills with physical, occupational and speech therapists
- Conference rooms and community rooms
Mill Creek provided equipment planning, initial outfitting, procurement, and warehousing for this replacement facility. In the design phase, Mill Creek worked hand-in-hand with the design team and user groups to verify layouts of key clinical spaces, define requirements for each space, create and review equipment lists with each department, discuss manufacturers and models, and confirm any equipment being reused. During the construction phase, we refined design documents and made final adjustments.
For procurement, we worked with the procurement team to identify any preferred /sole sourced vendors, as well as any group purchasing agreements already in place. We used the University of Nebraska Medical Center’s procurement standards to create a seamless process of equipment submittals and approvals before any equipment was released for purchase. Initial outfitting activities included oversight of the delivery, assembly, and installation of all FF&E items, including those delivered and installed directly by an equipment vendor.